Energy Efficiency - the MIWE way
"When our customers succeed, we succeed", is one of the central guidelines that governs the work at MIWE. This two-part philosophy works in many combinations such as, “If the environment succeeds, we succeed!” With one of the most important topics of the 21st Century in mind, i.e., the current climate crisis, it is clear that sustainability is a huge responsibility for each and every one.
MIWE has been working hard to improve the myriad aspects of sustainability for more than 13 years and over the last decade, its tenet has been to focus heavily on optimising the energy efficiency of all its products. The result has been a huge success for the environment, society and customers. Nevertheless, being sustainable is not only about energy efficiency; it is also about a strategic combination of the myriad tasks required to be carried out to attain specific CO2 emission targets, whilst also striving to achieve perfectly baked products. These targets being sometimes reached through radical modifications to process technology from raw material stage and kneading, proving right through to baking, packaging and delivery etc., against a backdrop of the often repeated upper global temperature, with 1.5°C in mind.
MIWE offers different solutions to tackle the important challenges for customers and the environment, whether their requirements include the improvement of energy consumption, CO2 reduction or sustainable production. Since it is always a good idea for equipment suppliers to improve their own in-house efficiency values themselves, MIWE began optimising its own energy consumption before offering this as a service to customers.
Since 2008 the company has been tracking the energy savings of all its products that have been sold and comparing it to previous statistics, whilst adding the values of all the energy recovery systems installed for customers, factoring in the savings at both MIWE locations in Germany. As of November 2021, savings add up to more than 71,000 tons of CO2 and over 277,000 megawatt hours of energy savings.
Starting the sustainability process in an organisation
Sustainability is best achieved by amassing the disparate and numerous measures into one portfolio. When it comes to energy savings, many bakers wonder, “Is it worth it?” After all, it is often believed that no one will invest in an energy recovery system that doesn’t provide tangible benefits and a return on investment. And MIWE agrees: a commitment of funds for such an undertaking, the size of which may not be insubstantial, must pay dividends with the money being spent on new systems being balanced by energy savings (ROI) in the shortest time possible. Whilst capital recovery is a major decisive factor, there are many other considerations to include.
Baking Europe carried out an energy recovery case study in the summer 2015 issue of the journal, at a bakery in Germany – click on this link for more details.
The cost argument
Energy is a relatively expensive commodity to bakers whatever the size of their operation, due to the nature of the business and with the cost of gas and electricity rising steeply (at the time of printing), it reinforces the argument of reducing energy consumption where possible, which will not only save money, but also reduce C02 emissions. In addition to baking ovens, cooling and freezing units consume a great deal of energy, so the annual gas, oil and electricity bills will add up to substantial costs. Whilst this may sound obvious, energy-use optimisation is, of course, the solution in order to produce goods of the highest quality with the lowest costs possible, once all other essentials have been considered.
A simple solution you might think, but mapping out such a project whilst under pressure to conform to government targets, can cause rash (and possibly very expensive) decisions to be made. Carpenters have a maxim, "measure twice, cut once" – decisions on major capital investments outlined here may be better placed by modifying this statement to, "measure thrice cut once"
The '$64,000 question'* is, therefore, what is the best way to reduce bakery energy costs? There are many options some of which are shown below:
[*Title of an American TV game show from the 1950s]
- Energy saving oven technology - Use energy more efficiently; an old, badly maintained burner will make poor use of fuel and moreover, be very inefficient. Investing in a new system can result in substantial savings and will more likely than not offer the same performance, (and equal or even better baking results) with a potential 30% reduction in energy. The best energy saved, is of course, the energy not used. Planned maintenance programmes, (where burners, light bulbs elements etc. are replaced at regular intervals en masse, regardless of wear) can sometimes appear to be wasteful, however, it is well documented that when energy consumption figures are analysed, the overall costs are lower than they would have been otherwise
- Clever energy recovery - Waste heat that is generated during baking, cooling and freezing shouldn’t be allowed to vanish unused through the flue or into the air; instead, it should be put to use in a targeted fashion to reduce energy costs in other parts of the building or operation.
- Combined heat and power generation (CHP) - CHP is an efficient process that generates electricity by harvesting waste heat that would otherwise be lost and that can be used elsewhere in the process or in the factory; a system that if integrated into the energy mix can help reduce energy use and associated costs.
- Alternative Energy - Careful consideration should be given to alternative fuels (such as biogas, wood pellets, or wood chips). These four components represent the foundation of the work done by MIWE energy, a service which, when employed, assesses the energy efficiency of a customer’s systems and components, the waste heat use in baking ovens and cooling units, the combined generation of heat and warmth and the use of optional extra, renewable energy sources to a bakery operation. These factors must all be taken into account to create a customised solution concept; one which will significantly reduce energy costs while maintaining product quality and processes. Of course, the investment returns that can be achieved by energy optimisation are dependent on individual specific circumstances.
The daily hours of operation of the units play an important role, as does the product portfolio and the current (and future) organisation of operations and processes. Not every solution will yield the desired result.
The environmental argument
There is no need to be an environmental activist to recognise that wasteful use of fossil fuel reserves will result in two serious problems. Firstly, the reserves are finite and the supply is shrinking. Over time, this will make fossil fuels increasingly scarce and more valuable and thus more expensive. However, the supply will eventually be exhausted. Secondly, as is well known, the harmful emissions that result from industrial applications, particularly those from the burning of fossil fuels, cause permanent damage to the environment, the effects of which are obvious and apparent all over the world. Anyone who saves energy is also conserving their reserves as well as helping the environment. This argument alone has convinced many bakers to implement energy optimisation, as has environmental awareness, which is fast becoming a powerful sales message: an increasing number of consumers are eager, not only to support energy-saving initiatives, but also to turn away from producers that rebuff the mounting global climate problems.
The legislative argument – ignore the energy crisis at your peril!
If the narrative thus far surrounding the recent COP26 conference and the current climate crisis has not yet convinced some bakery manufacturers of the benefits of investing in energy-saving solutions, then whilst this is the worst case scenario, impending legislative initiatives will be the shot across the bows. This may well be what is needed to overcome their resistance to change, as would possible enforcement measures. COP26 has also shown that politicians and many non-governmental organisations are raising awareness of the situation and are increasingly issuing or supporting strict rules and regulations to that effect.
Conclusion
In the future, the use of fossil fuel will be restricted to the operations and processes that cannot survive without it. Excess energy consumption will be branded as wasteful and governments will implement tax, political or legislative instruments that will make such waste increasingly expensive or ban it altogether. The question of how bakeries can reduce their energy consumption will, in the future, become a matter of public debate. In some European countries and in many sales operations, it has become common practice to indicate the quantity of emissions that arise from the entire manufacturing chain of a product.
As Peter Drucker is purported to have said (although the origin the quote is a still a subject of debate) - "Innovate or die", meaning, "stay ahead of the game or go under."
The intelligent energy recovery systems in the MIWE eco: range (depicted is a MIWE eco:nova in combination with three different oven types) offer maximal energy production and can be combined to create customised solutions for any bakery.
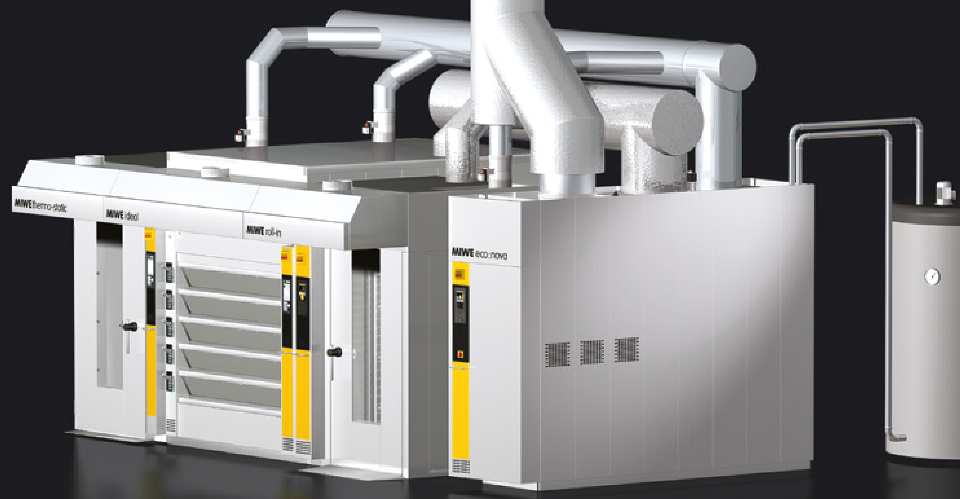
2729