Most food processors require a metal detector to comply with food safety standards and ensure complete product safety and quality. Although your metal detector may be "ticking all of the boxes", if it's not working to the optimum sensitivity specification, then metal contamination could be passing through your production line undetected.
Sensitivity is the measure of a metal detector's ability to detect a specific type and size of metal contaminant, and is a key contributor to the effectiveness of your metal detection program. The better the sensitivity of the metal detector, the smaller the pieces of irregular-shaped metal it can detect.
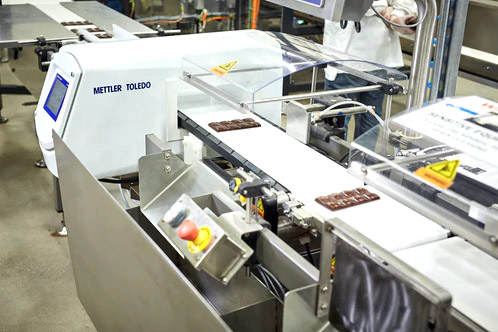
METTLER TOLEDO's conveyorized metal detection systems can inspect chocolate bars before or after final packaging
How is metal detector sensitivity measured?
The sensitivity of a metal detector is measured using certified test pieces. A test piece typically consists of a metal sphere made from ferrous, non-ferrous or stainless steel - the metal types most commonly identified via a HACCP analysis as likely contaminants in food.
Sensitivity should always be measured at the centre of the metal detector's aperture, as this is the least sensitive point. When comparing the performance of different metal detectors, the clear winner is usually the one with the best spherical sensitivity across all metal types, when measured in the centre of the aperture. However, in some cases, it may not be so clear.
One metal detector could out perform the other on one metal type, and vice versa for another. In this case, calculating the 'mean sensitivity' is a more effective performance measure.
While sensitivity performance is important, equally so is the stability of the metal detector in 'real world' production environments. Varying product effects and fluctuating electromagnetic interference are significant factors that can impact performance. Without noise immunity and adequate detection thresholds, the risk of false rejects rises significantly.
Factors that contribute to metal detection sensitivity
There are a number of factors that affect the detection sensitivity of a metal detector, such as product temperature, packaging, and orientation on the production line.
How sensitivity impacts real-life contaminant detection
When measuring the sensitivity of a metal detector, a test piece must be reliably detectable when passed through the centre of the aperture of the metal detector. However, there is a significant difference between the test piece's spherical sensitivity and the length of an irregular-shaped or wire contaminant that can be detected. An experienced provider can help you select the right solution to overcome these challenges.
Operating at the highest spherical sensitivity level will provide maximum protection to your brand and company's reputation, by dramatically improving your detection capability to real-life contaminants such as wires and swarf and reducing your risk of a product recall.
The chart below shows how improving detection sensitivity by 25% (going from a ball size of 2.0 mm to 1.5 mm for example) will significantly improve the length of the wire that can be detected, and decrease the risk of undetected metal reaching, and potentially causing harm to, consumers.
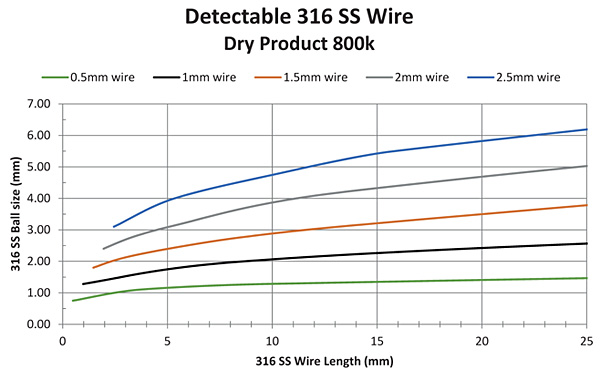
A small change in spherical sensitivity can make a big difference in wire length detection
How to achieve optimum operating sensitivity
To protect consumers, maximize efficiency and meet industry standards, manufacturers and processors have an important role to play in identifying, implementing and maintaining an optimum level of metal detector sensitivity.
Choosing a stable, reliable metal detector that delivers enhanced sensitivity levels is an integral part of a food safety program to minimize metal contamination going undetected.
However, having a metal detector is not enough – it must also be correctly installed, operated and maintained for optimal performance.
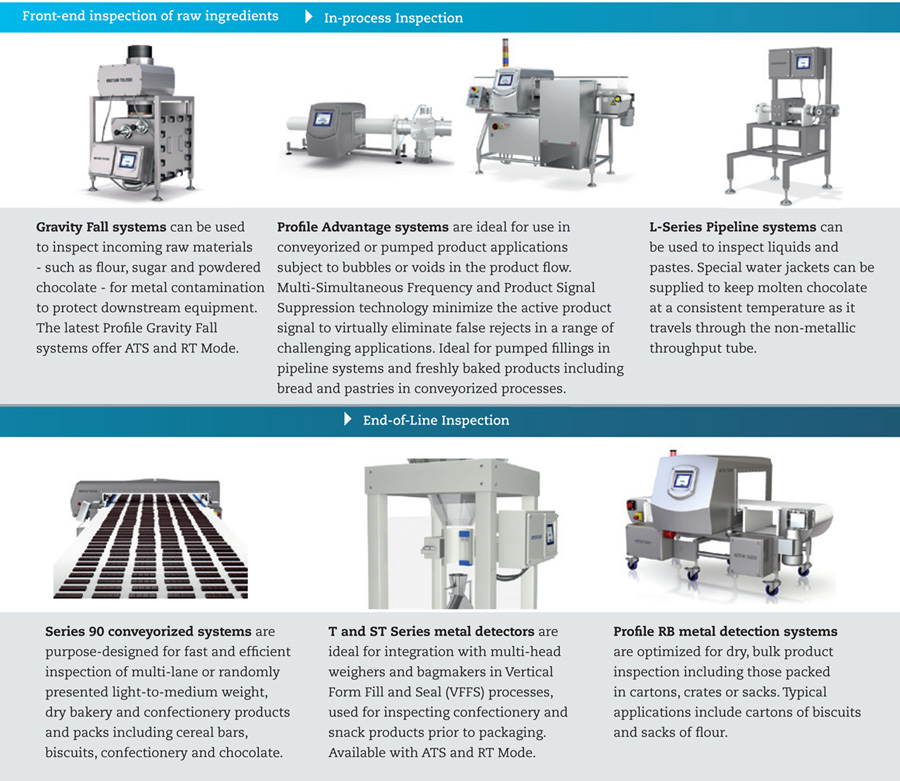
Chocolate Manufacturer Ritter Sport Enhances Quality Using Innovative Metal Detection Systems
German chocolate manufacturer, Ritter Sport uses metal detection systems from METTLER TOLEDO to reliably detect metal contaminants and remove defective products from the process at an important critical control point in production.
As the shape, size, and location of the potential metal flakes and splinters can vary greatly, Ritter Sport use metal detectors that are extremely sensitive. Relying on METTLER TOLEDO's ulta-high frequency Profile technology, these systems detect the smallest ferrous and non-ferrous fragments and stainless steel contaminants, regardless of their shape.
The operating frequency of the device can be individually configured, depending on the product to be inspected. Automatic Clustering allows products with similar product signal characteristics to be set up and grouped into one operational setting to remove the need for product changeover thus allowing downtime during a product change to be kept to an absolute minimum to help maintain OEE.
To read the full case study, visit: www.mt.com/md-ritter-sport